technology reshaping the construction industry
Edwin Warui
9 ways technology is reshaping the construction industry
According to McKinsey, the construction sector employs about seven percent of the world’s working-age population. But that’s not all. It’s also one of the largest sectors in the world with $10 trillion being spent every year on construction-related goods and services.
The challenge?
Some construction companies are still stuck in the old way of doing things. Spreadsheets, manual data entry and mountains of paperwork.
With all the technological advances happening around us, the construction industry has been slower in adopting technology. Consequently, it’s one of the least digitized sectors in the world.
The result?
Over the past two decades, construction productivity has averaged one percent annually compared to 2.8 percent in the global economy, or 3.6 percent in the case of manufacturing.
That said, there are real and practical applications of how technology is helping construction companies remain competitive. So let's look at some examples.
#1. Construction Site Robotics
It’s a familiar story and it usually goes like this: Robots are coming to take away our jobs.
But, that’s only half the story. On the flip side, robots improve speed and the quality of work. For instance, repetitive tasks such as bricklaying and tying rebars can be done by robots. Using a combination of artificial intelligence and robot vision, these machines save time, minimize wastage and allow workers to focus on complex tasks. Also, they help prevent injuries and can address labor shortages.
Now imagine this:
You report to your job site with just an ipad and some packed lunch. Next, you find a quiet spot to sit down, take out your ipad, open an application and voila! The excavator powers on and starts excavation without an operator. Sounds like fiction, right?
Wrong. It’s now being done. Just like self-driving cars, autonomous construction machinery is a reality. They allow the same amount of work to be done using fewer workers.
Equally important, construction involves a lot of heavy lifting. To help eliminate fatigue and boost productivity, robots come in handy. As a result, they keep human workers out of harm’s way.
#2. Wearables
This is technology that can be worn as an accessory, or even embedded in clothing. With the help of other technology such as augmented reality, then they can collect data in the workers’ environment. As a result, wearables can greatly improve risk management and safety in construction.
For instance, Shimabun, a Japanese company released an upgrade kit that can be used on standard hard hats. The kit has temperature and motion detectors that detect the exact location of workers, whether they are light-headed, or if they have fallen. This way, this technology reduces the risk of accidents and even if it does happen, it can be detected and help provided soonest possible.
Another example is Workersense. In addition to helping detect and prevent accidents, these wearables can tell your team’s work time and rest time to determine efficiency.
#3. Building Information Modeling (BIM)
Picture this:
According to McKinsey, large projects typically take 20 percent longer than expected to finish, and worse, are up to 80 percent over budget.
Normally, project managers have to deal with more than two different systems. This causes fragmentation of data and increases downtime between activities. As a result, wastage happens, budget overruns, and increased likelihood of disputes which further eats up valuable time.
The solution?
Building Information Modeling. This is a 3D modeling tool that brings together architecture, engineering and construction professionals for effective design, planning, construction, and maintenance of buildings and their infrastructure.
A single source of truth allows the collection of project information in one place. You communicate better. You know what’s happening in the field at any single time. In that case, you have more control, you avoid time-consuming claims, and you cut out admin workload such as unnecessary meetings, reports or even phone calls.
The good news is that the use of BIM has been mandated in the UK for government construction projects. The administration believes it will help them achieve its target of 15-20% savings on the cost of projects.
#4. Health and Safety Trackers
Construction is chaotic, and it’s the ultimate goal of every contractor to ensure that each worker returns home safely. But that’s not always the case.
According to UK’S Health and Safety Executive’s (HSE) 2019/2020 figures, in construction there were 61,000 cases of non-fatal work related injuries. In other words, that’s around 2.8 percent of workers in this industry suffering from an injury. Notably, this is significantly higher than the all industry rate of 1.8 percent.
Technology can help reduce injuries in construction sites. Using motion sensors one can detect accidents such as falls, or even head bumps. You can also tell in real-time when workers are close to danger zones such as high-noise areas. Additionally, you can tell when a worker enters an area they are not certified to enter. Consequently, you ensure workers are where they are supposed to be working.
#5. Virtual Reality(VR) and Augmented Reality(AR)
Virtual reality is a type of technology whereby the user is completely immersed in a computer generated reality that completely shuts out the physical world. Augmented reality on the other hand involves adding digital elements in the real world. VR for instance, was common in the gaming industry, but it has gradually infiltrated other sectors such as construction. Let’s see exactly how this works.
First, 3D VR modeling is being used to bring projects to life. Simply, you virtually walk through a project. It’s an immersive experience for a client as they get a feel of what the project will look like once it’s completed. This is because projects can be intimidating on paper for the untrained eye.
And if you’re selling housing units, then VR is a game changer. It allows you to stand out and have an edge over your competitors. The reason?
By enabling walkthroughs, virtual reality increases the chances of a client developing an emotional connection with a house. And since the majority of our decisions are controlled by emotions, then it’s easier to make a sale. To put it into perspective, according to Coschedule, people make 35,000 decisions per day, and emotions play a role in a staggering 90% of their day.
On the other hand, augmented reality can be helpful to your workforce. Workers can achieve more, gain confidence, and operate safely and on time. For instance, let's say you're dealing with specialized machinery and it unfortunately breaks down. It’s a special kind of machine and this kind of repair is beyond the experience of your technicians. The catch?
Restoration can only be done by a specialist who is miles away and would have to travel. Normally, this could mean project delay or worse, additional costs. The good news is that you can avoid all these inconveniences.
Using AR, it’s now possible to connect remote technicians to subject matter experts. Simply, the expert guides the technician/remote worker one-on-one without leaving the office. As a result, AR eliminates unnecessary travel, it fosters knowledge transfer between the expert and the remote worker, and tasks are completed accurately.
Finally, if you have a vacant site, then AR allows the completed project to be overlaid on the empty site so that the client can visualize the final result. Additionally, you could even make risk assessments by using hazard simulations.
#6. Remote Site Inspection
What if you could check the progress of your project without visiting the job site?
Well, it’s doable. Whether at home or the golf course, you can virtually walk to your jobsite. This way you can monitor progress, resolve issues and ensure quality.
And it gets even better. In 2018, the construction sector saw a 239 percent increase in the adoption of drone technology. The reason? Drones can be used in construction sites in various ways.
First, surveyors can use drones to survey a site in a matter of minutes. Ordinarily this would take weeks or even months with a crew on the ground. And what’s better? It ensures accuracy. The data collected can then be used to create 3D topographical maps or even make volume measurements.
Second, drones allow construction managers to have a quick view of the site without being physically present. This technology can also be used to safely check high-reach places such as tall buildings and bridges.
And lastly, drones are being used for on-site security. This minimizes theft hence keeping projects on schedule and at cost.
#7. Machinery Performance Management
Equipment is a large part of any construction project. You want them in the right location and functioning properly. But let’s be honest, keeping all the machinery, vehicle and heavy equipment properly managed is a tall order.
So how do you ensure optimal usage?
Enter technology. With technology you can have detailed records of your equipment, vehicles, fuel usage and maintenance all in one place. For instance, trucks and equipment can be fitted with real-time GPS for monitoring. This way you ensure safety and productivity, resulting in both time and money savings.
#8. Quality Assurance
Quality assurance is a set of processes that ensure that quality standards are adhered to. The goal is to ensure that the resultant project is in line with the design. Solid quality assurance practices are critical in ensuring that expensive delays don’t occur when things don’t go according to plan.
For example, concrete is at the heart of many construction projects. You need to make sure the mix-design is correct. And second, that the concrete is of the right strength. A small deviation in mixing and the correct strength won’t be achieved. The result? Additional costs if you have to redo concrete casting.
With technology, it’s now possible to monitor concrete behaviour. Be it concrete strength, temperature or humidity. This way, problems are detected early hence minimizing waste and delays.
#9. Offsite Construction
Off-site construction may either be prefabricated or modular. In prefabricated construction, building components such as door assemblies, floor assemblies, and wall panels are made off-site then transported to the construction site to be assembled.
Modular construction on the other hand, can involve complete rooms with finishes and fixtures already installed. They are then transported to the construction site and installed. These modules can then be used to assemble larger units such as hostels and apartments faster, cheaper and efficiently.
And another thing. Offsite construction is steadily gaining traction. McKinsey estimates that the market value for modular construction in new real estate construction alone could reach $130 billion in Europe and the United States by 2030. Equally important, according to a report by KPMG, seven percent savings was possible when applying offsite construction.
With shrinking working spaces and more stringent safety and environmental standards, offsite construction is becoming necessary. For instance, 3D printing offers immense potential. This technology allows prefabrication offsite and then the materials are transported to the job site ready for use. Time is saved and there’s improved sustainability in the production process.
Talking of sustainability, did you know that construction produced 120 metric tons of wastage (59 percent of total UK waste) in 2014? Well, according to the UK Green Building Council, this equates to 30 percent of construction firms pre-tax profit.
Bringing it all Together
If you think about it, the construction sector is always adopting technology. A century back there were no power tools. If you wanted to do excavations you would have to use pickaxes and shovels. Heavy construction machinery was unheard of.
Even today, technology will keep evolving and the construction industry will advance in the tools, processes, and materials it relies on. It’s an ongoing process and no one knows how far it will go. We will keep pushing the limits of human ingenuity.
Construction companies that are adopting technology are reaping rewards through increased productivity, completion of projects on time and on budget. The result? Higher profit margins. And isn’t that the dream?
technology reshaping the construction industry
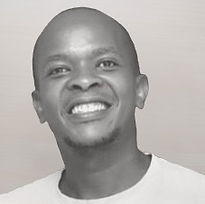